|
ACCESS THE FULL ARTICLE
No SPIE Account? Create one
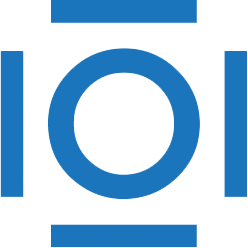
CITATIONS
Cited by 4 scholarly publications.
Silicon
Plasma etching
Etching
Plasma
Optical lithography
System on a chip
Directed self assembly