|
ACCESS THE FULL ARTICLE
No SPIE Account? Create one
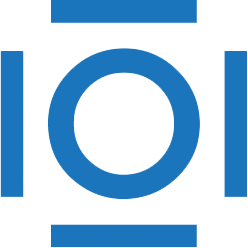
CITATIONS
Cited by 3 scholarly publications.
Optical alignment
Chemical mechanical planarization
Polishing
Semiconducting wafers
Etching
Scanning probe microscopy
Oxides