|
ACCESS THE FULL ARTICLE
No SPIE Account? Create one
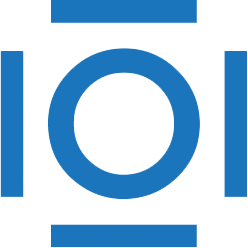
CITATIONS
Cited by 17 scholarly publications and 9 patents.
Line width roughness
Photoresist processing
Image processing
Double patterning technology
Particles
Photomasks
Semiconducting wafers