|
ACCESS THE FULL ARTICLE
No SPIE Account? Create one
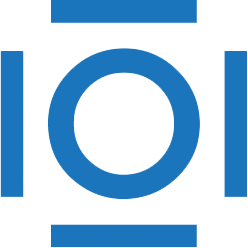
CITATIONS
Cited by 1 scholarly publication.
Process control
Particles
Control systems
Process engineering
Manufacturing
Semiconductors
Data processing