To remove these smaller dimension errors with a conformal tool is impractical. The preferred approach therefore is to apply a sufficiently rigid tool of sufficient size so that it preferentially removes material from the peaks and not from the valleys. A larger tool is capable of smoothing surfaces where the peaks are further apart and also benefits from a larger removal rate, reducing the total process time. To achieve a uniform contact the form of the tool should be the inverse of the local form of the surface. This is trivial for spherical or plano surfaces, but present problems when the surface is aspherical. The mismatch between a rigid tool and the workpiece increases with the size of the tool for a given asphere, which leads to an upper limit of the tool size that can be used. The work reported in this article presents a numerical analysis of the mismatch of rigid tools applied on E-ELT prototype segments. It can be readily applied to aspheric or free-form surfaces for which an analytical approach is difficult or impossible and furthermore it provides a detailed analysis of the form of this mismatch, including spatial frequency content. Additionally, an analysis and experimental work is presented to determine the applicability of sub-aperture rigid tools for the polishing of E-ELT segments. |
ACCESS THE FULL ARTICLE
No SPIE Account? Create one
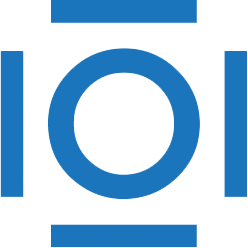
CITATIONS
Cited by 1 scholarly publication.
Polishing
Surface finishing
Mirrors
Aspheric lenses
Prototyping
Telescopes
Photovoltaics